Zur additiven Fertigung von Kunststoffbauteilen hat sich das filamentbasierte Verfahren Fused Filament Fabrication (FFF) etabliert. Jedoch treten in diesem Prozess hohe thermische Energieverluste durch konvektive Wärmeströme auf, die kompensiert werden müssen, um auch Hochleistungspolymere in hinreichender Qualität verarbeiten zu können.
Das Projekt verfolgte das Ziel, die konvektiven Energieverluste im FFF-Verfahren unter Hochvakuumbedingungen möglichst zu eliminieren, sodass die im Stand der Technik nötige Temperierung der Bauraumkammer entfällt.
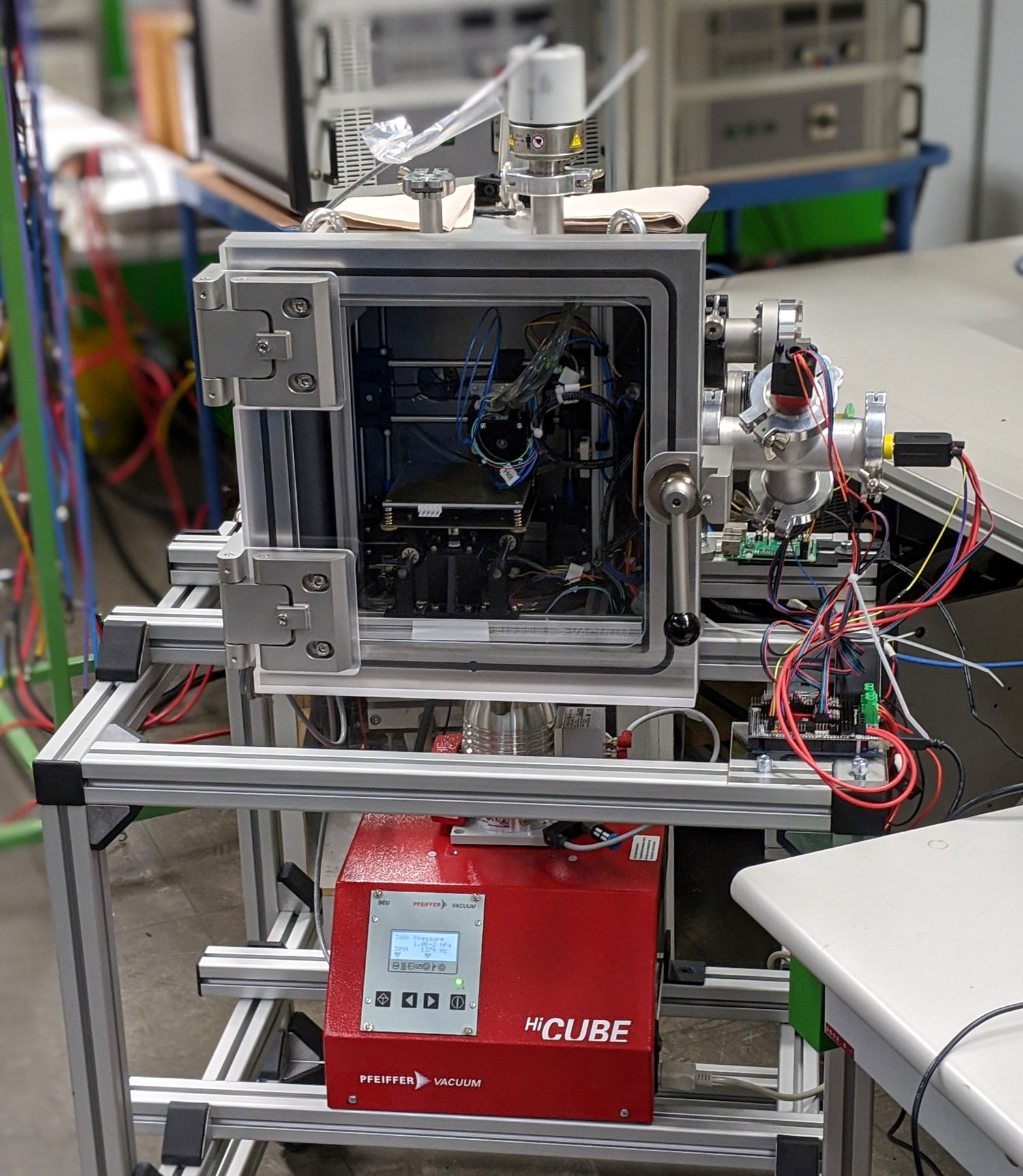
Es wurde ein Labormuster einer vakuumkompatiblen FFF-Anlage konstruiert und aufgebaut. Diese Anlage wurde anschließend in eine Hochvakuumanlage integriert. Zur Überwachung der Thermalprozesse wurde zudem eine Thermalkamera installiert, mit der die Temperaturen des Druckkopfes sowie die des ausgetragenen Filaments aufgezeichnet werden können. In der Vakuumkammer wurde die FFF-Anlage erfolgreich bei bis zu 10-4 hPa betrieben.
Abschließend konnte in diesem Projekt der Betrieb eines filamentbasierten 3D-Druckers im Hochvakuum erfolgreich demonstriert werden. Zur Prozessvalidierung wurden Probekörper nach der DIN EN ISO 527 in drei Raumorientierungen gefertigt und in Zugversuchen geprüft. Dabei konnte kein signifikanter Unterschied zwischen den Zugstäben, die an der Atmosphäre, und den Zugstäben, die unter Vakuum gefertigt wurden, festgestellt werden. Somit konnte gezeigt werden, dass die additive Fertigung von Kunststoffbauteilen ohne Verluste in der Zugfestigkeit unter Vakuumbedingungen möglich ist.